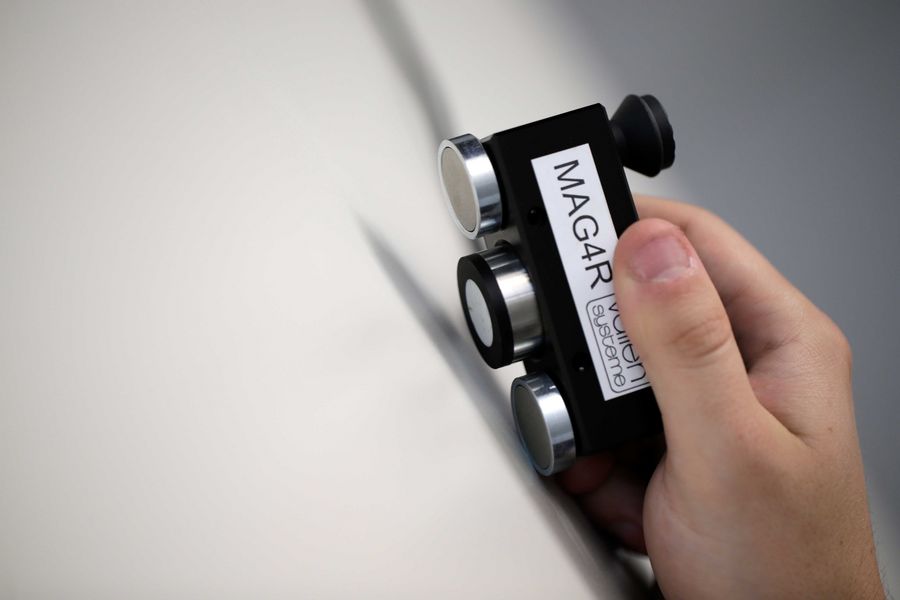
Der Gesetzgeber schreibt die regelmäßige Überprüfung von Druckgeräten vor, um Mängel und Materialermüdung frühzeitig zu erkennen. Damit werden Unfälle, Explosionen und Lecks zuverlässig verhindert, die Mensch und Umwelt ansonsten in Gefahr bringen können.
Das „Gesetz über Überwachungsbedürftige Anlagen“ verpflichtet Betreiber von Druckgeräten zur wiederkehrenden Prüfung. Die Betriebssicherheitsverordnung (BetrSichV) regelt die Anwendung von Arbeitsmitteln, um Mitarbeiter und Personen im Umkreis zu schützen – daraus ergeben sich Anforderungen an die wiederkehrenden Prüfungen von Druckanlagen und ihren Teilen.
Sicht-, Ultraschall-, Röntgen-, Druck- und Leckageprüfungen gehören zu den gängigen zerstörungsfreien Prüfverfahren für Druckgeräte. Ergänzend kann eine Schallemissionsprüfung (SEP) durchgeführt werden: Sie erlaubt es, Materialermüdung in Form von Rissen und Rissbildung, Korrosion, Leckagen und plastische Verformung sowie Reibung zu detektieren und zu lokalisieren. Damit können Schäden besonders früh erkannt und gegengesteuert werden, bevor sie ein kritisches Stadium erreichen.
Schallwellen im Material der Druckbehälter
Anders als bei Ultraschallprüfungen, wo eine Schallwelle ins Material geschickt wird, wird bei der Schallemissionsprüfung das Material des Behälters unter Last gesetzt: In der Regel wird das Eigenmedium – etwa Gas oder eine Flüssigkeit – bis zum gewünschten Prüfdruck eingeleitet. Die Geräte müssen also häufig nicht geleert werden, was den Aufwand – zeitlich, organisatorisch und monetär – minimiert. Schäden wie Risse oder Leckagen geben unter dem Druck Schallwellen im Ultraschallbereich in der Wandung des Behälters ab, die von piezoelektronischen Sensoren detektiert werden können. Ihre Piezo-Kristalle bestehen aus besonderen Materialien wie Quarz oder Keramik und besitzen die notwendigen piezoelektrischen Eigenschaften: Sie erzeugen eine elektrische Spannung, wenn bereits kleinste mechanische Einwirkungen wie Druck oder Zug auf sie ausgeübt werden. Die so erzeugte Spannung wird im Sensor als Messsignal umgesetzt. Das Messsystem filtert aus diesen Signalen Informationen heraus: die maximale Amplitude der Schallwelle, also der Moment des höchsten Schalldrucks, seine Energie, die Zeit von der Erkennung bis zum maximalen Ausschlag und die Dauer. Anhand dieser Merkmale werden Signale beurteilt und ausgewertet.
Weil der Schall die Sensoren zu unterschiedlichen Zeitpunkten erreicht, können Signale anhand der Laufzeitdifferenz genau geortet werden. Das Wissen um den Ursprung des Geräuschs ist wichtig, da es Auskunft über die Bedeutung gibt: Bei der Druckprüfung dehnt sich der Behälter – die Bewegung kann beispielsweise zum Scheuern auf seinen Auflagern führen. Auch dieses Geräusch nehmen die Sensoren wahr. Lässt es sich nun lokalisieren, ist schnell klar, dass es sich dabei nicht um einen Riss an einer kritischen Stelle wie einer Schweißnaht handelt. Während der Prüfung kann der Behälter durch die Platzierung der Sensoren zu 100 Prozent überwacht werden, was eine genaue Beurteilung erlaubt.
Normen und Grenzwerte
Bei Ultraschallprüfungen legen Normen fest, wann eine Fehleranzeige noch zulässig ist. Faktoren sind hier unter anderem Wanddicke oder Echo- beziehungsweise Amplitudenhöhe. Bei der Schallemissionsprüfung gibt es keine konkreten Grenzwerte; die Norm gibt lediglich vor, welche Werte aufgezeichnet werden müssen: Signalrate als Funktion von Zeit und Last sowie die Amplitude als maximaler Ausschlag des Spannungssignals über der Zeit. Die Quellen der Geräusche müssen geortet und zugeordnet werden. Eine weitere Norm gibt vor, aufgrund welcher Parameter die Signale beurteilt werden: Auch hier gibt es keine Grenz- oder Schwellenwerte, stattdessen nennt die Norm Beispielwerte. Ein wichtiger Anhaltspunkt sind hohe Amplituden, die mit viel Energie korrelieren, was ein genaues Hinsehen erfordert. Konkrete Richtwerte muss sich jede Prüforganisation, die Schallemissionsprüfungen durchführt, selbst erarbeiten und damit interne Kriterien entwickeln.
Messung und Ergebnisse der SEP
Für Schallemissionsprüfungen sind Umgebungsgeräusche, Material und Wandstärke, Geometrie und Medium wichtige Einflussgrößen. Prüfer müssen berücksichtigen, dass Störgeräusche von Leckagen bei einer Prüfung von Anfang an vorhanden sein oder durch die Druckeinwirkung erst entstehen können. Ebenso müssen die Prüfer Auflagergeräusche und die Geräusche von nebenstehenden Maschinen erkennen und abgrenzen können. Mögliche Schäden sind zudem unterschiedlich laut: Um zum Beispiel Risse erkennen zu können, müssen vor der Prüfung Ventile und Dichtungen geprüft und bei Bedarf nachgezogen oder erneuert werden – sonst würden dort mögliche Leckagen die Geräusche des Risswachstums schlicht übertönen. Auch die Detektion von Korrosion ist herausfordernd: Der chemische Prozess und das Abplatzen von Materialschichten sind zwar hörbar, aber leise. Um deren Begleitgeräusche aufzunehmen, benötigen die Sensoren eine niedrige Resonanzfrequenz – und sind deswegen empfindlich auf Störgeräusche aus der Umgebung, etwa Wind und Regen.
Ein weiterer Faktor ist die Wandstärke: In einem dünnen Material kann sich der Schall nahezu nur in zwei Dimensionen ausbreiten, in X- und Y-Richtung; bei einem Behälter mit einer Wanddicke von mehreren Zentimetern ist eine voluminösere Ausbreitung in drei Richtungen möglich – der Schall verläuft sich dann schneller im Material; außerdem kann es zu Reflexionen und Interferenzen kommen. Hier sind mehr Sensoren notwendig und ihre Auflage muss genau geprüft werden. Befindet sich ein flüssiges Medium wie Wasser oder Öl im Behälter, wird die Schallwelle im Vergleich zu einem gasförmigen Inhalt gedämpft, auch hier sind mehr Sensoren notwendig.
Dass nach Schallemissionsprüfungen Behälter nicht mehr weiterbetrieben werden dürfen, ist selten. Die Behälter sind in der Regel so konstruiert, dass sie höheren Belastungen als im täglichen Betrieb üblich standhalten, etwa durch Korrosionszuschläge in der Wandstärke. Manchmal ergibt sich sogar eine Entwarnung, etwa, wenn ein Behälter Signale im Bereich einer sensiblen Rundnaht zeigt und durch eine Folgeuntersuchung mit Ultraschall dann erkannt wird, dass es sich um noch zulässige Ungänzen, etwa aus der Herstellung handelt.
Die Einrichtung der Software
Beim zugelassenen Prüfbetrieb TÜV Hessen wird für die Messung in der Prüfsoftware ein Modell des Behälters erstellt, auf dem die Lage der Sensoren vermerkt ist. Damit erkennen die Prüfer, wo genau im Behälter ein Signal entsteht.
Die Softwareeinstellungen müssen für eine Prüfung stets angepasst werden, wobei der Aufwand variiert: Die Anpassung für einen standardisierten, zylindrischen Druckbehälter ist schnell ausgeführt; die Sensorzahl ergibt sich aus Umfang und Durchmesser und oft lassen sich Einstellungen aus vorangegangenen Prüfungen ähnlicher Behälter übernehmen. Oft sind die Geometrien von Anlagen aber kompliziert und weisen mehrere zylinderförmige Behältnisse auf. Dann gestaltet sich die Einrichtung der Software aufwändiger.
Zugelassener Prüfbetrieb als Partner
Die SEP kann bei Druckgeräten, die nach der Betriebssicherheitsverordnung wiederkehrend geprüft werden müssen, als Sonderprüfverfahren für die Innenbesichtigung im Rahmen der inneren Prüfung oder für die hydrostatische Festigkeitsprüfung eingesetzt werden.
Es ist sinnvoll, dass ein zugelassener Prüfbetrieb wie die Technische Überwachung Hessen GmbH die Prüfungen organisiert, koordiniert, durchführt und dokumentiert. Das Personal ist nach EN ISO 9712:2022 qualifiziert und besitzt die nötige Erfahrung und Expertise im Bereich der zerstörungsfreien Prüfung. Zudem ist es von Vorteil, wenn der Partner alle notwendigen Bereiche abdecken und aus einer Hand anbieten kann; TÜV Hessen etwa kann ebenfalls die Festigkeitsprüfung und innere Prüfung bescheinigen und falls notwendig, Folgeprüfungen, wie Ultraschallprüfungen etwa an Schweißnähten in die Wege leiten und durchführen. Damit muss keine weitere Firma mit ins Boot geholt werden, was Verzögerungen wie Wartezeiten auf Dokumente von einem Sachverständigen vermeidet. TÜV Hessen erklärt bei Bedarf auch die möglichen Prüftechniken und Sonderverfahren, etwa den Einsatz einer Ultraschallkamera zur Detektion von Leckagen, die auch ergänzend zur Schallemissionsprüfung durchgeführt wird.
Unternehmen reduzieren damit Kosten und Zeit für die Vorbereitung und die Durchführung der Prüfung. Dabei kommt stets der Stand der Technik zum Einsatz, welcher valide Ergebnisse liefert. Die Schallemissionsprüfung ist nicht nur für Druckgeräte ein geeignetes Verfahren, sondern generell für beanspruchte Bauteile und Strukturen. Auch besteht die Möglichkeit, mit der Schallemissionsmessung ein Monitoring einzurichten, um somit eine Struktur permanent überwachen zu können.
Fazit
Mit der Schallemissionsprüfung und ihren empfindlichen piezoelektrischen Sensoren können wachsende Risse im Material von Druckbehältern früh erkannt werden. Die SEP eignet sich deswegen als Ergänzung und gegebenenfalls Ersatz zu wiederkehrenden zerstörungsfreien Prüfungen und kann durchgeführt werden, ohne dass der Behälter geleert werden muss. Empfehlenswert ist es, die SEP von einem zugelassenen Prüfbetrieb durchführen zu lassen, der das entsprechende Know-how sowie die nötigen Ressourcen mitbringt, um mit diesem das vollständige Prüfprogramm reibungslos durchzuführen.