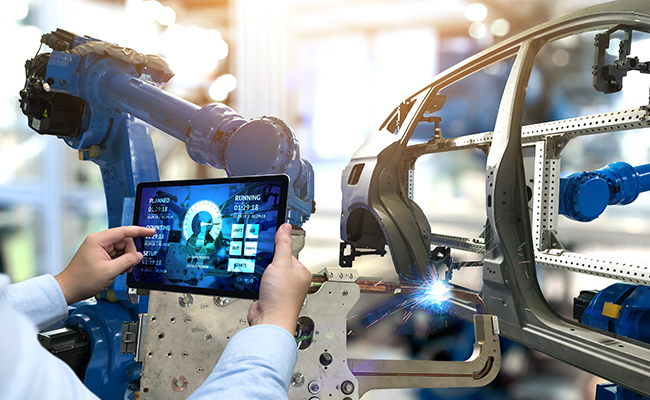
Der Begriff Industrie 4.0 feiert Jubiläum. Weltweit ist Industrie 4.0 in den vergangenen zehn Jahren zu einem Synonym für die Digitalisierung der Industrie geworden. Doch ist der runde Geburtstag auch ein Grund zum Feiern? Eine Zwischenbilanz.
Das Schlagwort Industrie 4.0 wurde 2011 als branchenübergreifende Strategie für produzierende Unternehmen eingeführt. Der Begriff sollte Hersteller auf dem Weg in die digitalisierte Zukunft begleiten. Das Ziel ist eine smarte Fabrik, in der flexibel, dynamisch und effizient gearbeitet wird. Weltweit vernetzte Maschinen und Anlagen sollen Bedarfe schnell bedienen, auf potenzielle Ausfälle reagieren und idealerweise mit Lieferanten und Kunden online kommunizieren können.
Vier grundlegende Prinzipien sollten die Industrie 4.0 definieren. Das erste Prinzip der Vernetzung beschreibt die Kommunikation von Maschinen, Geräten, Sensoren und Menschen im Internet der Dinge. Im zweiten Prinzip der Informationstransparenz entsteht mit Sensordaten ein virtuelles Bild von digitalisierten Fabriken. Die technische Assistenz bildet das dritte Prinzip. Assistenzsysteme unterstützen dabei den Menschen mit aggregierten, visualisierten und verständlichen Informationen. Dezentrale Entscheidungen sind das Ergebnis des vierten Prinzips. Digitalisierte Systeme treffen eigenständige Entscheidungen, um Aufgaben autonom zu erledigen.
Wachstum im Internet der Dinge
Mit den wachsenden Möglichkeiten vernetzter Anlagen entstehen eine Unmenge neuer Herausforderungen. Das britische Marktforschungsunternehmen IHS Markit rechnet bis 2030 mit einem Anstieg auf 125 Milliarden digital vernetzter Geräte im Internet der Dinge. Und jeder digitalisierte Prozess treibt die Entwicklung weiter voran und generiert zusätzliche Chancen: von der günstigen Produktion niedriger Stückzahlen für individuelle Kundenwünsche über mehr Arbeitssicherheit dank neuer Assistenzsysteme bis zu mehr Nachhaltigkeit in energieeffizienten Fabriken.
In den vergangenen zehn Jahren seit dem Start der Industrie 4.0 hat sich schon viel getan. Viele Anwendungen haben sich seither etabliert, die 2011 gerade erst entwickelt wurden. Datengesteuerte Prozesse oder prädiktive Instandhaltung gehören in vielen produzierenden Unternehmen längst zum Alltag. „Die Industrie 4.0 ist eine sehr gute Chance, um sich mit richtigen und gezielt eingesetzten Investitionen nachhaltig Wettbewerbsvorteile zu erzielen“, sagt Jürgen Bruder, Mitglied der Geschäftsleitung von TÜV Hessen. „Kein Wunder, dass seit 2011 unglaublich viele Ideen, Konzepte und Umsetzungsstrategien entstanden sind.“
Nachholbedarf an vielen Stellen
In manchen Bereichen ist die Entwicklung in den vergangenen zehn Jahren bereits weit fortgeschritten. Glaubt man verschiedenen Analysen, besitzt die Digitalisierung der Industrie auf Managementebene höchste Priorität. Laut einer Studie des Digitalverbands Bitkom aus dem Mai 2020 sehen 94 Prozent der Entscheider in der Industrie 4.0 eine Voraussetzung für die Wettbewerbsfähigkeit der deutschen Industrie. Die gleiche Studie ergab, dass in sechs von zehn Unternehmen bereits spezielle Anwendungen für die Industrie 4.0 genutzt werden.
An anderen Stellen besteht hingegen noch Nachholbedarf. Gerade in mittelständischen Unternehmen der produzierenden Industrie ist der Weg zur smarten Fabrik teilweise erst am Anfang. Der Verband Deutscher Maschinen- und Anlagenbau e.V. schätzt, dass in den Betrieben 85 Prozent der Bestandsanlagen noch nicht vernetzt sind. Experten gehen davon aus, dass es derzeit noch an der flächendeckenden Digitalisierung mangelt und Industrie-4.0-Anwendungen bisher hauptsächlich Insellösungen sind.
Als größtes Hindernis der erfolgreichen digitalen Transformation gelten laut Bitkom-Studie hohe Kosten für die notwendigen Investitionen und Sorgen um Datenschutz und Datensicherheit. Während es für die erste Hürde mittlerweile kostengünstigere Lösungen gibt, die sich relativ schnell rechnen, sind die verschiedenen Aspekte der Informationssicherheit oft eine Frage des Vertrauens. „Insbesondere mittelständische Unternehmen haben häufig Bedenken, ihre Daten Partnern, Dienstleistern oder Zulieferern zur Verfügung zu stellen“, bestätigt Jürgen Bruder. Zu groß ist die Sorge, dass der Wettbewerb Zugriff auf die wertvollen Informationen gewinnt.
Index gibt Orientierung
Eine weitere Hürde für eine erfolgreiche digitale Transformation ist die fehlende neutrale, produktunabhängige und professionelle Entscheidungsgrundlage. Viele notwendige Prozesse sind für Entscheider schwer skalierbar, weshalb die Beantwortung der Frage, wie die digitale Transformation systematisch eingeleitet und nachhaltig gestaltet werden kann, zu oft aufgeschoben wird. Gleichzeitig steigt der Druck, die Digitalisierung in den Betrieben voranzutreiben, um wettbewerbsfähig zu bleiben. Strukturiertes Vorgehen ist an dieser Stelle gefragt, um nicht in Rückstand zu geraten.
Bei der Entwicklung der passenden Industrie-4.0-Strategie werden unterstützende Tools benötigt. Das Weltwirtschaftsforum empfiehlt den Smart Industry Readiness Index (SIRI), der in Singapur entwickelt wurde. Mit der Hilfe von erfahrenen Experten kann in einem Assessment der Status quo ermittelt und die Zukunft geplant werden. Für die Realisierung der folgenden Schritte wird ein realistischer Fahrplan mit konkreten Zielen inklusive einer unabhängigen Bewertung erstellt, um die notwendigen Investitionen abzusichern. Denn die Implementierung vieler digitaler Veränderungen steht in vielen Betrieben noch aus. Doch die Zeit drängt. Um als produzierendes Unternehmen auch in zehn Jahren weiter erfolgreich zu sein, muss die digitale Transformation eingeleitet werden.
Hinweis: Wir übernehmen keinerlei Haftung für die Inhalte und Aussagen auf externen Seiten. Bei Beanstandungen wenden Sie sich bitte an den Urheber der jeweiligen Seite. Vielen Dank für Ihr Verständnis.